SLE: Selective Laser-induced Etching (also known as ISLE: In-volume SLE)
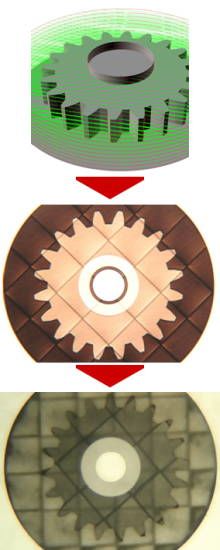
Selective laser-induced etching (SLE) is a two-step process to produce 3D structures in transparent materials (also known as ISLE: In-volume selective laser induced etching - to distinguish our process from laser ablation):
In a first step the transparent fused silica glass is modified internally by laser radiation to increase the chemical etchability locally. To prevent the formation of cracks in the brittle material short pulse duration (fs-ps) and a small focal volume (a few µm3) are used. The focus is scanned inside the glass to modify a 3D connected volume with contact to the surface of the workpiece.
In a second step the modified material is selectively removed by wet chemical etching resulting in the development of the 3D product. Essential for the precision of the SLE technique is the selectivity. The selectivity is the ratio of the etching rate of the modified material and the etching rate of the untreated material. The selectivity in fused silica glass is larger than 500:1 resulting in long fine channels with small conicity (picture below). Therefore, by the SLE-technique complex 3D cavities can be produced, which are the basis of our products like micro fluidic structures and micro structures 3D parts.
During the laser treatment no material is removed but modified in the structure. Therefore, the SLE-process is not suitable for in-line processing. The workpiece must be removed from the machine to be developed in a separate bath and newly aligned for further processing.
Advantages of SLE are the large precision (~ 1µm), no debris, true 3D capability and the high processing speed using our micro scanners. Therefore, the SLE technology is perfect for digital 3D printing of glass components.
